Product Hub May 25, 2015
A Warped View of Printing
Advice and secrets from the screen printing know-it-alls.
We warped a print a few weeks ago and had to set up the job again to print one piece for a good customer who had to have a small order perfect. We put too much adhesive on the platen and warped the print when we yanked it off the press.
Those of you out there that have never had that happen? Liars! It happens to all of us, and we struggle mightily to avoid it. Some tips:
- If you put too much roll-on adhesive or too much spray tack on, put a shirt or two on and pull them off before you try an important print for real.
- Don’t use the cheapest crap you can find. That is penny wise and pound foolish. I would say that at least 25% of the shops I go into are using sub-standard adhesives. If you use bad glue, you are going to have registration problems, ink won’t release properly from the screens and you will have to spray or roll on more adhesive, which is both wasteful and makes a mess.
- Don’t be tempted to print a few more pieces when you know you need to re-apply adhesive. That shirt that comes loose will make a big mess. It isn’t worth it.
- Don’t use crappy spray tack. It will get all over your machine, and it will cause registration problems. Try and avoid spray as it is wasteful, expensive and makes a mess of your machines and shop. Your employees hate it for good reason. Use roll-on when you can and good spray when you have to. – RR
Project Management
“Digitizing” the presses has been on my projects list for years now. It’s quite the undertaking, but once completed, it will allow us to digitally display the full and accurate range of on-press screen and platen movement in relation to each other and in relation to screen profile and artboard. (These components we have already digitized.) This is a big deal for us as we run so many designs comprised of oversized prints, non-standard placements, and non-standard garments (garments are digitized on an ad hoc basis). A tremendous amount of time will be saved in design development by working within these parameters visually on screen rather than having to take garments to press and record physical measurements in every instance.
This is a multi-phase project, of course, but we started by measuring all unique platen styles/sizes, including specific measurements for width, length and height as well as press compabitility. Eventually every platen will be issued a unique ID and labeled accordingly. We will also photograph the platens, which will be used to accurately vectorize each unique platen style and size in inventory. While we were at it, we decided to document inventory and clean. More to come on this project. – TD
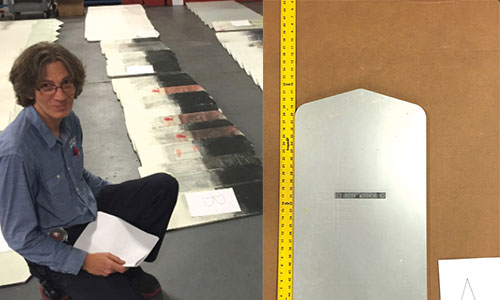
Tom Davenport is founder and president of Motion Textile, Inc. (asi/72662). He currently serves on the Board of Directors for SGIA.
Rick Roth is the president of Mirror Image Inc. He is known for his award-winning screen printing and embroidery as well as his philanthropy. Visit The Ink Kitchen blog at www.theinkkitchen.com.
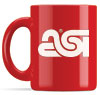
Product Hub
Find the latest in quality products, must-know trends and fresh ideas for upcoming end-buyer campaigns.