Product Hub May 26, 2014
Tri, Tri, Tri Again
Bright prints, soft hand on tri-blends – can it be done?
John Wilhelmsen has owned and operated Distinct Impression, Inc. since 1979. The Tucson, Arizona-based shop dabbles in several facets of screen printing, including custom printing and industrial printing for the aerospace and medical industries. Besides his apparel quandaries (expanding his selection of Made-in-USA garments, finding stylish T-shirts that fit his boomer clientele), Wilhelmsen is looking for the best way to print plastisol on tri-blend. “Half of our business is contract printing,” he says, “and many times tri-blends, modal or poly viscose shirts are in the same order as 100% cotton shirts. I have observed that I lose print quality when printing these shirts with plastisol inks.” Wilhelmsen is interested in maintaining brightness while keeping the hand light, and wants to know if an additive or some additional trick is required for the ink.
Mixing It Up
Tony Kozlowski, the owner at T Productions, sees a fair share of tri-blends come through his shop. His company uses a custom white ink, made mostly with a low-bleed plastisol with 20% super poly thrown in. “This is our day to day white,” says Kozlowski, who is based out of Mishawaka, IN, “as so many garments these days have some sort of man-made material in them.” T Productions uses it for everything from 100% cotton to 50/50s to tri-blends. For 100% poly garments, the shop uses just the Super Poly White.
“Some shops opt for three or more white inks for different usages,” says Kozlowski, ticking off a few common plastisol variations: nylon, low-bleed for 50/50s, super poly for 100% synthetic and a standard white for 100% cotton. “But we have narrowed it down to two.” The reason is simplicity. It eliminates the chances of the using the wrong white, and allows for consistency across all facets of its process instead of switching between thick and thin inks. The low-bleed properties of Kozlowski’s everyday white won’t have a major effect on the cotton tees he prints, but it won’t hurt them either. “It’s OK to overuse low bleed, but not so much to under-use it these days,” he says. And while there are cost savings to 100% cotton white, that can go out the window on a botched 50/50 print.
With dark tri-blends, Kozlowski definitely recommends a low-bleed white for the dark fabric, especially as an underbase. Wilhelmsen has openly wondered about the addition of an additive, but Kozlowski says additives like Catalyst or Nylobond should only be used on nylon jackets, where elasticity is not needed. In addition, he suggests a crush plate to use while the underbase is hot that will crush the fibers back into the ink deposit.
To preserve the fashion angle of the tri-blends, Wilhelmsen typically uses a fine mesh, either 280 or 305, “to lay down as little ink as possible, he says. “[But] we appear to lose ink brightness when printing on these fabrics.” Kozlowski thinks that mesh “is way too high to lay enough ink down to successfully print ‘bright’ on these fabrics.” If a bright print is the goal, he suggests a maximum of 158 mesh for the underbase, perhaps even 110 or 86 if the art allows. If a fashion look with little hand is the aim, the higher mesh is the way to go. “This mesh/look/feel struggle has been going on as long as screen printing itself,” Kozlowski says. “Modern man-made textile materials have forced printers to adapt and often sacrifice hand for brightness.”
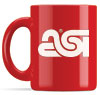
Product Hub
Find the latest in quality products, must-know trends and fresh ideas for upcoming end-buyer campaigns.