Product Hub July 24, 2014
Dirty Jobs: Uniforms Edition
When it comes to apparel, you’ll find one thing at the intersection of presentation and protection: uniforms. They are essential for businesses to show a polished, professional image, and yet they need to be rugged and durable to handle the toughest of jobs. Our Dirty Jobs series, inspired by the Discovery Channel show of the same name, profiles workers who know the value of hard work – and being prepared for whatever filth comes their way.
Public Works
Beware of exploding paint cans, food waste and soiled diapers. By Theresa Hegel
Chris Nicol and Mike Warden, employees of the town’s public works department, jump off to fling a haphazard pile of plump bags from the curb into the truck’s hopper. When the back is full, Nicol flips a switch, and the truck’s heavy packer blade descends. The dark green bags hiss like slowly deflating balloons as they’re squished; then, in an instant, the plastic bursts, sending plumes of chalky ash into the air.
That’s the moment you have to watch out for, Nicol says. You never know what surprises are lurking in someone else’s garbage. On several memorably messy occasions, Nicol’s uniform was spattered with the smelly shrapnel from an exploding diaper. Another time, he recalls getting hit with a mint-hued mist when a can of spray paint succumbed to the packer blade. “I was like the Hulk, all green on my face,” he says. “Stuff like that explodes here and there.”
On wet days, gritty, gray garbage water squirts from the truck as the trash is compressed. Nicol and Warden say they learned early on to stand off to the side and not directly behind the hopper, but if there’s a change in the wind, it can be hard to avoid the splash zone. In the heat of the summer, it’s the smell that’s most difficult to deal with, “You get used to it, but some stuff’s really bad,” Nicol says.
Perkasie’s public works crew collects garbage four days a week, rotating the three-person job among a staff of 10, according to Dan Gilbert, the director of public works. The crew picks up around eight tons of trash a day, and on Fridays they pick up recyclables.
Trash duty is probably the dirtiest part of a public works employee’s job. But the rest of the time is no walk in the park, either. Well, except for when it is: The department is in charge of maintaining Perkasie’s extensive park system, weeding and mowing 130 grassy acres. The crew also takes care of the public swimming pools and keeps the town’s streets clear and in good repair. Climbing down into storm sewers and shoveling out leaves and muck clogging the drainage system is another messy aspect of the job, Gilbert says.
Working outside in all weathers requires access to a range of uniform options. Perkasie employs Clemens Uniforms, based in nearby Lansdale, PA, to supply and launder their garments. Crew members can choose between heavy-duty work pants or knee-length shorts in warmer weather. They have button-down collared shirts made of moisture-wicking performance fabric, with a logoed patch sewn on the chest. Or, workers can wear neon yellow T-shirts with the logo of a leafy tree and the words “Perkasie Borough” printed on the chest. The crew also receives jackets with zip-in liners for warmth. Heavy-duty boots and work gloves with finger grips round out the look. Public works employees say they’ll wear out a pair of gloves every two weeks to a month, depending on the kind of work they’re doing.
Back on the cul-de-sac, Warden and Nicol hoist a discarded gas grill off the sidewalk. Red-brown grit spills onto the street as they tip the bulky barbecue into the hopper. “This will make some noise,” Warden predicts. Sure enough, the grill squeaks and pops alarmingly as the metal crumples under the force of the packer. The men watch, undeterred, as it’s flattened, then hop back onto the truck to head to the next stop on their route.
Animal Shelter
Taking care of animals is a dirt ‘breeding’ ground. By Sara Lavenduski
Like many of the animals admitted to the Bucks County SPCA in Lahaska, PA, Duchess’ exact breeding couldn’t be ascertained. But it didn’t matter – she was a mother-to-be in need, and the staff took her in and helped deliver seven healthy puppies. For socialization purposes, they’re placed in a playpen in the middle of the facility’s administrative area. They wobble around, bumping into each other with barely opened eyes, practically begging to be scooped up and cuddled. But Nikki Thompson, director of education & outreach, delivers a warning spoken with the authority of almost 10 years’ experience: “As soon as you pick one up, there’s something running down your leg.”
Caring for animals in need is a rewarding job, as any of the 15 staff members and almost 100 active volunteers at this SPCA location will attest. But it’s also a dirty one. Hair, fur, vomit, saliva, dirt, mud, nail clippings, blood, excrement, water, even parasites – all are common materials with which staff and volunteers come in contact on a daily basis. “Everyone brings extra clothes every day, just in case,” says Thompson.
At any one time, the workers care for approximately 20 to 30 dogs, a slightly higher number of cats, and small animals, including rabbits, ferrets, chinchillas, parakeets and parrots. Services include admissions, adoptions, 24-hour emergency assistance and cruelty investigations that involve four humane officers.
Tasks at this SPCA location range from complex grooming and bathing sessions to thorough cleaning of the facility. The worst arises during rescues from hoarder homes. “We don’t have much warning when we have to go into those situations,” explains Amanda Dubell, a kennel technician. “We don’t always know what we’re getting into, so we wear paper masks, shoe covers and work gloves or rubber gloves. We’ll often just wear the same clothes from that day because there isn’t a whole lot of time, and when we get back we change into our extra clothes for the rest of the day.”
Frank Nassetta, a staff member with seven years’ experience, is responsible for maintaining the main kennel, building and grounds. “Our clothes really go through the wringer,” he says as he holds a large Lionhead rabbit that scratches at his branded polo and leaves behind a significant amount of fur. “They wear out in a matter of months, especially the tops. They get clawed, pecked and stained, and we wash them constantly.”
Dubell says they only wear closed-toe shoes, either sneakers or workboots, and jeans on the job. “Denim is not only durable,” Thompson agrees, “but it also provides the best protection.” Workers aren’t required to wear a specific top, though it should be comfortable and easy-care. Staff and humane officers receive polos from JERZEES (asi/84257), screen-printed with a subtle, one-color print on the left chest, and volunteers often wear DryBlend T-shirts from Gildan Activewear SRL (asi/56842) with a large logo on the front. In the fall and winter, NuBlend sweatshirts from JERZEES with the same full-front imprint come in handy. “We avoid stiff-looking uniforms,” says Thompson. “Some of the dogs, depending on past experiences, are actually afraid of them.”
Because of the fast-paced environment at the SPCA, one basic outfit has to take wearers through a multitude of tasks, hence the comfort and easy-care recommendations. Says Dubell, “each day is unpredictable, and our clothes have to keep up.”
Wildlife Removal
Wild and dirty takes on a whole new meaning for these animal pros. By Chuck zak
Wildlife isn’t just in the wild. It’s probably in your chimney, too.
If you’re in the Philadelphia area and the great outdoors has gotten a little too indoors for comfort, you have a few options. The bad ones involve shimmying painfully through tight spaces, manic screaming and a lot of broken housewares. The good option is to call A Wildlife Pro, a wildlife removal company who will extract the offending critter with far less drama and damage – but still an impressive amount of dirt and sweat.
Based in suburban Montgomery County, A Wildlife Pro is led by Philadelphia native Kris Baccari and a small, tight-knit team which includes his wife Shannon. Their list of services runs long, but it all involves reluctant animals, tight spaces, heat, dirt and … well, other stuff. “We do attic cleanouts where we get copious amounts of bat guano,” Baccari says. “You’re talking a tremendous amount of buildup where we have to take out all the insulation. The amount of spores and fibers that are just everywhere is just absolutely awful.”
For these especially grueling jobs, Baccari and his crew need to be fully “Tyvek’d up” along with respirators and gloves. Inside that sheath of Tyvek, Baccari is clad in his omnipresent A Wildlife Pro T-shirt with silkscreened logo on front and “Wildlife Removal” on the back. Favoring the Beefy all-cotton tee from Hanes (asi/59528) in earth-color tan or olive-drab green, Baccari usually brings along a “backpack full of shirts” that he draws from during a long day. “I‘ll go through two or three shirts depending on how much I sweat,” he says. Those tees lucky enough to survive the ordeal go back to Baccari’s home where they get washed separately on a heavy cycle.
As a 24/7 operation, the always-on-call company never lets their professional image slip, donning their logoed shirts even during late-night calls. “I like people to know what I do,” Baccari says. “I feel that it’s very important.”
The relief of his customers is a big reason for the warm acceptance Baccari receives wherever he is operating. The services A Wildlife Pro offers – dirty and fraught with potential danger – are not those the average homeowner wants to tackle on their own, such as crawling up into a chimney flue to reach a trapped animal. “Raccoons will nest on the flue and squirrels fall down the chimney and can’t get back up,” Baccari explains. “The only way of getting them out is by pulling your body into the cavity of the flue and hand-grabbing them. And that is filthy.”
A quick wash down with dish detergent usually follows Baccari’s excellent adventures, though there are some jobs that might make even that claustrophobic journey seem relatively tidy.
“Sometimes we get called to mobile home parks where something has died up underneath the trailer,” Baccari says. Though this may seem a fairly easy bit of critter extraction, thick and heavily-insulated vapor barriers designed to protect pipes from freezing surround many of these homes and make the process considerably more challenging. Crawling underneath may be unrealistic for anyone not of a dangerously slight frame, but there is another solution. It requires a strong stomach, however. “You have to feel around for a hot spot or a spot that’s moving and filled with maggots and you have to cut that spot out,” Baccari says. “And if you make a bad cut, you’re in trouble, because that’s just dripping all over you.”
A Wildlife Pro is scrupulous about the treatment of the animals it captures, and is proudly “100% humane.” It’s all part of the guiding philosophy that Baccari sums up thusly: “If we can’t do it, nobody can.”
Uniform Rental Company
Fighting a clean fight against the grubbiest apparel. By C.J. Mittica
For businesses that are involved in the dirtiest of jobs – grease, sludge, blood and much more – a clean uniform is just one delivery away. No more thought required.
They rely on companies like UniFirst, which has garnered over 260,000 business customer locations nationwide by succeeding at, among other things, one major task: figuring out how to get grimy uniforms clean. At the company’s Croydon, PA plant, all it takes is 145 employees, 90,000 gallons of water a day and 600 gallons of detergent per month to complete the job.
If you’re looking for soot and dirt here, you won’t see it for long. It sits at one end of the facility (one of UniFirst’s three largest in the U.S.) with each day’s deliveries of used items – uniforms, yes, but also shop towels, aprons, floor mats and much more. “All the dirty work is done back here,” says plant manager John Burns. He walks through the plant on a hot early summer morning amid bins of soiled garments. The items are sorted by type and nature of soiling, weighed meticulously and then hoisted away. In the well-aired plant, smell is not an issue. But sometimes return deliveries can bring the most unwelcomed surprises, like a long-unopened bag that Burns had to pry into. “It had to be the worst smelling thing I’ve smelled in my life,” he says, “and I’ve been working here for 35 years.”
What you won’t smell is bleach, detergent, or any typical cleaning odors you might suspect to find in a robust laundry operation. UniFirst relies on a liquid injection system that delivers precise, computer-controlled cleaning detergent formulas based upon specific types of soils and garments. The workers at the ISO 9001:2008 certified Croydon plant input one of nearly 50 unique formulas into the microprocessors at each washer. The concentrated doses of agents hygienically clean monstrous loads of laundry – up to 675 pounds in fact – in UniFirst’s state-of-the-art industrial washing machines that reside in a “Wash Alley.”
Precision is key. An overloaded washer won’t leave enough room for the clothing to “flip” adequately, leaving the chance for permanent “shock wrinkles.” The wrong formula or the slightest imbalance in pH can damage the fabric. “The process is like one big chemistry set,” says Rich Powell, the plant’s general manager, who started as a part-time high school worker 35 years ago.
After the wash, the company’s 600-lb dryers finish the job. (No surprise – there’s a lot of lint and loose change.) For most people at home, the laundry process ends here. But UniFirst services industries where presentation is everything. So the company ushers each garment through a 10-point quality inspection process, searching for any defects like missing buttons or ripped seams. About 4% of the garments get put aside for repairs. All UniFirst work shirts and lab coats are also professionally pressed for a crisp and polished business image. “We’re one of the only uniform providers to meticulously press our industrial shirts and medical coats at no charge,” says Burns. Other garments are put through a steam tunnel to take out their wrinkles.
Automation carries the garments the rest of the way. Heat-sealed bar code labels on the inside of shirt and jacket collars, as well as pant waists, are scanned, sorted by delivery day and route, and then by company. In a couple days’ time, they are out the door for the once-a-week delivery to UniFirst’s clients.
Cleaning uniforms is not all that happens at the 56,000-square foot facility. The plant carries 31,000 pieces of inventory for new garments, along with company logos and emblems to be sewn on. While items are available for purchase, the vast majority of items are slated for uniform rentals, UniFirst’s primary business. A rental program allows companies to let UniFirst supply and maintain all workwear for low weekly charges, with no upfront costs. The price is minimal compared to buying; in fact, Powell says prices have has actually come down over the last 30 years. The amount of dirt, on the other hand, has not. For dirty work around the country, businesses turn to UniFirst for a clean slate.
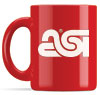
Product Hub
Find the latest in quality products, must-know trends and fresh ideas for upcoming end-buyer campaigns.