Product Hub October 29, 2014
Mending the Apparel Trade
It’s been a year and a half since a factory collapse in Bangladesh killed more than 1,120 people, most of them garment workers. Some in the industry believe this preventable tragedy was the wakeup call needed to usher in an era of ethical sourcing, but they say there’s still a lot of work to be done in Bangladesh – and the rest of the world.
Apparel maker David Bebon has been involved in Bangladesh’s garment industry since the late 1980s – back when the country’s nascent cut-and-sew trade was, as he says, “pretty much the Wild West.” He remembers inspecting factories with his father and seeing fire escapes dangling dangerously from the outer walls of buildings, threatening to buckle under the slightest of weights. One factory they walked through had designated an internal stairway as its “fire escape.” The owner didn’t understand at first why Bebon’s father thought that wasn’t such a good idea.
To Bebon, CEO of 5-year-old DBEBZ Apparel, those anecdotes are not about pointing the finger at a country that’s had long-standing compliance problems. Instead, they’re object lessons in why it’s important for apparel suppliers to take an active role in ensuring their garments are being made in safe and socially conscious facilities. “My personal feeling is we need to take a responsible stance in the entire supply chain,” he says.
Last April, a deadly building collapse in Bangladesh sparked a global outcry at the lack of oversight, dangerous conditions and disregard for workers’ health and safety in the country’s $23 billion garment industry, which employs more than 4 million. But, experts warn, it’s a mistake to think this is just Bangladesh’s issue. Instead, they say, it’s indicative of our “fast fashion” culture that expects $10 T-shirts, no matter what, and an apparel industry always on the hunt for ever-cheaper labor to accommodate those demands. Bebon doesn’t mince words: “We’re used to the only product in the world that has gone down in price in 20 years. … The evolution of apparel manufacturing has always been and always will be to the lowest-cost place. … It’s just the way the industry works.” But, he adds, that doesn’t mean we should accept the loss of human lives as merely the cost of doing business.
The Aftermath of Rana Plaza
The Rana Plaza, built on swampy land outside Dhaka, was an eight-story building that was only approved to be five stories high. It collapsed last year, killing more than 1,120 people and injuring more than 2,500. Considered the deadliest accident in the world’s garment industry, it came just four months after a fire at the Tazreen Fashions factory in Dhaka killed 112 workers. A number of U.S. and European brands, including Wal-Mart, Sears and Benetton, were linked to the factories.
In the months that followed the Rana Plaza collapse, retailers formed two groups to inspect and improve factories in Bangladesh. The Accord on Fire and Building Safety in Bangladesh – composed of more than 150 apparel brands, mostly European – vowed to inspect about 50 factories a week. As of August, representatives say they’ve inspected more than 1,000 factories, publishing more than 150 corrective action plans online.
Wal-Mart and Gap were among the two dozen American and Canadian brands that created the separate Alliance for Bangladesh Worker Safety, which had a goal of inspecting nearly 600 factories. In May, the Alliance announced it had completed the first round of inspections, identifying problems such as poor wiring, lack of fire escapes and overloaded buildings.
Throughout the process, the two groups have butted heads with the Bangladeshi government, resistant factory owners and each other. “The Accord and Alliance are using the same tools, but they’re approaching the results differently,” says D. Fenton, executive director of the Quality Certification Alliance, a nonprofit group that helps promotional product suppliers provide safe and compliant products. They’ve “defined the issue differently, [so] it’s really hard to get a consistent set of directions out of that. We do know they’re raising the bar because they’re all attacking the problem,” she adds.
In August, the Accord decided to re-inspect the 300 or so factories used by both Alliance and Accord members, citing concerns that the Alliance’s inspections wouldn’t meet the Accord’s standards. In a statement on its website, Ellen Tauscher, Alliance chairwoman, called the Accord’s actions “a setback for garment safety efforts in Bangladesh.” The move also angered the country’s garment manufacturers, who have shut down nearly two dozen factories deemed unsafe by the groups. Shahidullah Azim, vice president of the Bangladesh Garment Manufacturers and Exporters Association, tells India’s Business Standard that the dispute has “hampered factory production and increased [the] cost of safety upgrades.” He also expressed confusion over which inspection report a factory is supposed to follow.
Despite the recent disagreements, many industry experts say the inspections are a good start, but, they stress, they’re only a start. The more difficult part is actually fixing all the safety issues uncovered during the walkthroughs, a point underlined by recent fires at two Accord-inspected factories. In late August, a fire at Cordial Design Ltd. in Mirpur, Dhaka injured five factory workers; the fire started in a detached storage facility the owners didn’t reveal to Accord engineers. In September, a fire at Mega Dyeing Ltd. in Gazipur left one worker dead and five others injured.
It’s also important to note that the Alliance and Accord have been monitoring only a fraction of the manufacturers in the country: “We’ve got [about] 5,000 factories in Bangladesh,” Bebon says. “My personal opinion: I bet 2,000 of them you could close tomorrow. … That’s good. Let them go away. … They need to clean up their act or go bye-bye.”
Around 218 garment factories have been closed in the year and half since the Rana Plaza tragedy, including the 20 or so recommended by the Accord and Alliance, according to Azim of the BGMEA.
Another point to consider: Though Bangladesh’s garment industry continues to grow, China still dominates the garment industry, and there are plenty of other countries with a cheap and abundant workforce gaining traction in the cut-and-sew trade. Why haven’t retailers embraced Accord or Alliance-style models to oversee their other factories around the world, asks Amrou Awaysheh, an assistant professor who studies supply chain and corporate social responsibility at Indiana University’s Kelley School of Business. The answer, he says, is that there haven’t been enough consumers demanding change yet. “If you were to ask anybody now, ‘Do you remember the Rana disaster?’ most people will probably say no. … Unfortunately, the only time things will change is when another disaster happens, and it’s on the news. … It will take something bad to happen in Malaysia for retailers to say, ‘Let’s do an alliance there,’” Awaysheh says.
Untangling the Supply Chain
Awaysheh believes the key to widespread substantive changes in global manufacturing is transparency throughout the supply chain. The rise of social media and viral video sharing has helped tremendously. “Five to 10 years ago the average person wouldn’t know what a supply chain is,” he says. “Now they realize things don’t magically appear on the shelf.”
Suppliers have traditionally been reluctant to reveal too much about sourcing strategies, often worried about losing a competitive advantage. That attitude has been changing, with many companies publishing a corporate social responsibility policy online and including at least a few particulars about where garments are made. Swiss apparel brand Switcher goes further than most. Eight years ago, the company began to include a “DNA code” on each garment, which buyers can enter into the website Respect-code.org to find detailed information on every step of the supply chain, from where the cotton was picked, spun and dyed, to how the finished garment was distributed, according to Switcher executive Gilles Dana. Most important, he says, is information on the certifications and audits of each facility involved in the apparel-making process.
“You can’t be sustainable if you only know something was ‘Made in Portugal,’” Dana says. “A T-shirt isn’t produced in only one factory. There are six to 10 steps. It’s too easy to say a factory is nice and clean, but maybe behind that step in the supply chain, there are very bad social or environmental conditions.”
Switcher has even invited some clients to tour the factories it uses, unafraid that this could lead a client to buy directly from that facility, instead of from Switcher. “We decided years and years ago to be transparent,” Dana says. “We won’t hide the truth. We don’t fear being copied, but open all the doors.” Corporate buyers, he adds, are willing to pay a little extra for the security a coded garment brings.
Even if a brand isn’t willing to go the Switcher route, its supply chain should at least be clear to its own executives. Retailers like Wal-Mart and Sears that were connected to the Tazreen factory claimed suppliers had subcontracted there without their knowledge. To Bebon, such a shady supply chain is unacceptable. “If you don’t know your product is in a factory, you don’t deserve my business,” he says. “You’ve got to know, and if you don’t know, then you shouldn’t be making shirts. You have to be responsible for your production. … You place a 40,000-dozen order with a factory, and you never looked at it?”
Georgeta Navodarszky, director of global sourcing at alphabroder/Ash City (asi/34063), agrees. “I have no idea how a sourcing executive would be able to allocate business without knowing the factory, or getting in close touch with the company owners. You can’t have other people do the diligence work,” she says. “There’s no factory that gets our business without us being there, auditing, getting the reference and doing the first trial order just to make sure that everything works fine.”
Independent Auditing Brands that don’t regularly visit their factories should use respected agents and insist on facilities that have undergone independent third-party auditing and have the certifications to prove it. The CEO of one of the most well-known groups, Worldwide Responsible Accredited Production (WRAP), says he’s seen an increase in requests for certification since the Rana Plaza disaster.
“With very few exceptions, you can’t expect these brands to be able to have their own set of eyeballs in each factory. It’s not resource-efficient because supply chains are very widespread,” says Avedis Seferian, CEO and president of WRAP. “You also want to make sure you have an independent verifier. There is, on the surface at least, a potential conflict because you have a vested interest in passing the factory because your product will be made in it. … We have no dog in the fight.”
Critics of factory auditing, however, point to situations like the 2012 fire at the Ali Enterprises Factory in Karachi, Pakistan. More than 260 textile workers died, trapped by barred windows and locked exits. Just weeks before the blaze, a respected factory monitoring group, Social Accountability International, gave the facility a prestigious SA8000 certification, saying it had met standards in areas including minimum wages, child labor and health and safety.
“It’s a cat and mouse game,” Awaysheh says. He gives a hypothetical, but often all-too-real example of a factory that keeps its fire escape chained to prevent workers from taking breaks. When an auditor is expected, “The owner unchains the fire escape, makes sure all the workers understand that, if asked, they say they have time off, take breaks and wear protective clothing. The inspector walks through and says it’s safe. You have hundreds of factories to inspect, so you move on. What do you think the owner does when the inspector leaves?”
Seferian agrees that WRAP and other auditing shouldn’t be done in a “gotcha environment.” It’s less about checking items off a list, and more about ensuring systems are in place to handle emergencies and educating manufacturers on their responsibilities, he says. “It’s not enough to just look around and see fire alarms, extinguishers and escapes. The real questions are: Are these exits always kept open? Are workers properly trained in knowing how to use them? Is there someone whose job it is to inspect those extinguishers?”
Like the Alliance and Accord, independent factory auditing is a positive first step in ensuring ethical sourcing. “You can knock WRAP all day long, but it’s something. It’s sending people in,” says Bebon. “We need more WRAP-certified factories, specifically in Bangladesh, Cambodia, China and Vietnam. There are many factories that would not pass WRAP, but they’re there doing business.”
Benefits of Collaboration
Something that should help dissipate the adversarial “cat-and-mouse” relationship between many suppliers and their overseas factories is to move away from a system of merely monitoring factory conditions, and toward one of collaboration among all parties, Awaysheh says. Think of monitoring as the stick rather than the carrot, with brands using the threat of pulling their business to force a factory to reform, he says.
Instead, suppliers and manufacturers would be better off working together to improve conditions. It’s about forming a relationship and building trust. A collaborative supplier might invest money in the factory, specifically to purchase protective equipment for workers – a move that would make employees safer and more productive and perhaps inspire the factory owner to invest more of his or her own money. “It’s a win-win-win across the board,” Awaysheh says. The catch? To work, collaboration requires a long-term view, and most brands are too focused on short-term goals to invest the necessary time and money on one particular factory, he says.
Still, more and more suppliers are seeing the benefits of a collaborative model. Fruit of the Loom (asi/84257), for example, received the 2013 Secretary of State’s Award for Corporate Excellence for a factory it opened in Honduras more than 20 years ago. “We’ve forged a ground-breaking collective bargaining agreement with the workers, and we recognize unions and have adopted a union-neutral policy at all of our assembly facilities in Honduras,” says Rick Medlin, president and CEO. The company has also provided more than 10,000 health screenings for the local Honduran community.
Last year, Boxercraft (asi/41325) started using Haiti-based factory Industrial Revolution II to manufacture 80% of its tops, with plans to increase overall orders in the future. The factory, backed by designer Donna Karan and actor Matt Damon, promises to train unemployed Haitians, pay them more than the minimum wage and donate half its profits to social programs. “This was the right thing to do,” says Shelley Foland, CEO.
The Good and the Bad
Though Bangladesh’s garment sector has become the poster child for labor abuses and industrial negligence, it’s not so simple as to write off an entire country as a bad place to do business. Experts say that’s the wrong message to take away.
There are many well-run and regulated factories in Bangladesh, with several manufacturers investing significant funds to build “green” factories that reduce water, energy and chemical consumption. “We’ve seen a lot of improvements in Bangladesh,” says Navodarszky of alphabroder/Ash City. “Unfortunately, some of the individuals and media in the industry may only focus on the exceptions and tragedy. We have to spread the good news as well, so at least customers gain more confidence in knowing that continuous improvements take place in most of the reputable factories.”
And there are many bad factories in countries other than Bangladesh, even in locations you might not expect, such as Europe and the U.S. Earlier this year, the Clean Clothes Campaign, a European group dedicated to improving conditions for global garment workers, released a study that uncovered poor conditions and poverty wages in many Eastern European clothing factories. According to the report, a group of Turkish workers admitted that they had to sign a clause not to get pregnant for five years in order to get jobs as garment workers. Other interviewed workers said they were unable to take days off from work or earn sick leave, and many mentioned being forced to work overtime, clocking 200 hours a month or more. “We expect garment workers in Asia are being exploited with low wages and poor working conditions, but what this report shows is that there are no good guys,” says Bettina Musiolek, a co-author of the Clean Clothes Campaign’s Stitched Up report.
The “silver lining in the very dark cloud” of the Rana Plaza tragedy, says Seferian of WRAP, is that it has raised the profile of socially responsible business practices in the industry. “We’re now in an environment where this is as much a part of the production process as checking for quality of the product,” he says. “It’s not an add-on or a niche. It’s part and parcel of doing business.”
The important thing, Bebon notes, is not to abandon Bangladesh, but to engage with the government and factory owners to continue to bring about change. If that means the price of a T-shirt has to go up by a dollar, he thinks it would be money well spent. “I believe the American consumer can afford that,” Bebon says. “We can’t let people die from making shirts.”
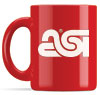
Product Hub
Find the latest in quality products, must-know trends and fresh ideas for upcoming end-buyer campaigns.